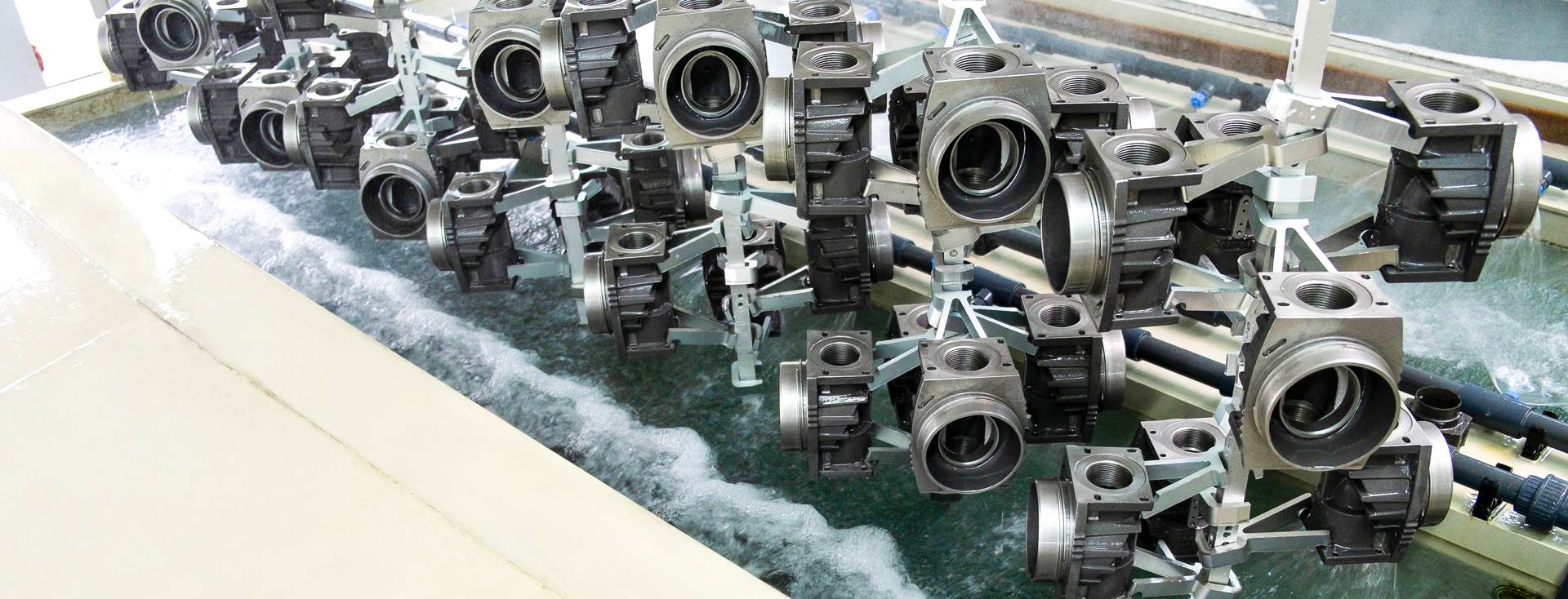
Surfactant concentration monitoring for industrial baths and electrolysis processes
Cleaning baths - Electroplating baths - Etching baths - Electrolytic metal refining
Surfactants perform important functions in industrial baths. In cleaning baths they are the effective component while acting as wetting agents in etching or electroplating baths to ensure uniform wetting of the entire workpiece. When gases are released, as in electroplating or in the electrolytic extraction and refining of metals such as copper, surfactants prevent the formation of toxic or corrosive spray mist (acid mist) by reducing the size of rising gas bubbles or by forming a foam carpet. To ensure that all these processes run optimally, the surfactant content must be checked at regular intervals.
Regular bath checks with a mobile bubble pressure tensiometer
The control should be carried out at close intervals in order to be able to react quickly if the surfactant concentration has fallen below a critical value. Otherwise, high costs can arise due to quality and time losses: The plant must be stopped for a longer period of time, foam or dirt must be skimmed off laboriously by hand and parts must be re-cleaned while the jobs are piling up.
Mobile solutions are ideal for monitoring, so that the surfactant content can be measured directly in the bath or on site after a quick sample has been taken. All this is accomplished by bath controls based on surface tension with a bubble pressure tensiometer.
Concentration measurement based on surface tension – a task with difficulties
The surface tension of surfactant solutions depends on the concentration; it is therefore obvious to also use this variable for bath control. Since the effect of the surfactants in the baths is also directly or indirectly related to the reduction of the surface tension, its measurement is a process-related variable. However, surfactants reduce surface tension only below the critical micelle concentration (CMC). Above this concentration, the surface is saturated with surfactant molecules and molecular aggregates known as micelles form in the solution. The surface tension remains constant and is no longer a suitable test parameter. At the same time, the surfactant content in industrial baths is almost always above the CMC.
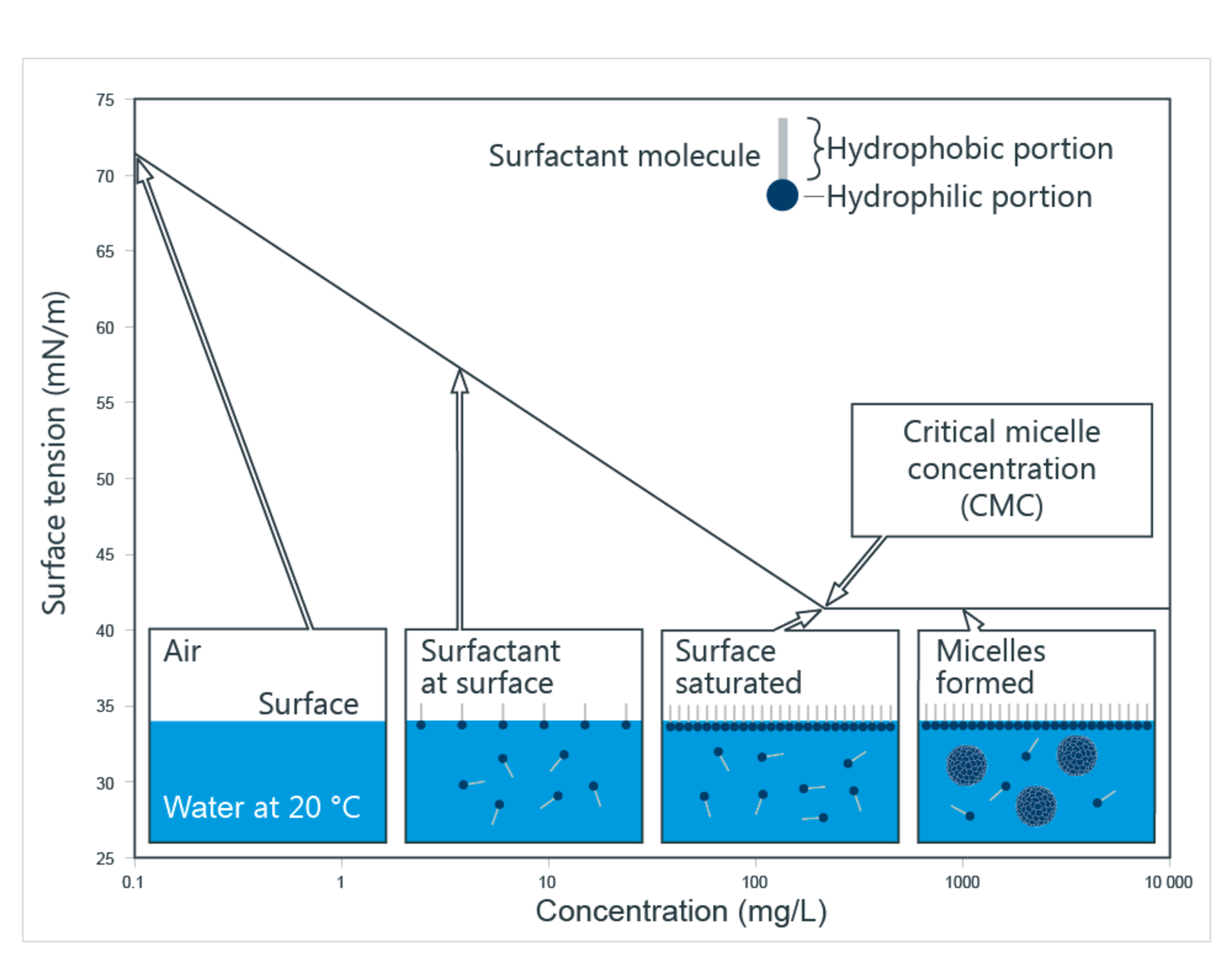
The solution: measurement of dynamic surface tension
The bubble pressure method is nevertheless suitable for bath control because it measures the surface tension of freshly formed surfaces where surfactant saturation has not yet occurred. This dynamic surface tension is strongly dependent on the surfactant concentration inside the solution, even above the CMC. The method is based on measuring the internal pressure of gas bubbles generated in the sample using a capillary. The surface age can be adjusted by varying the bubble formation rate over a wide range and optimized for the surfactant.
From the calibration curve to mobile single-point measurement
In order to use the bubble pressure method for bath control, a calibration curve is first created in the laboratory for the surfactant in question. Firstly, the exact correlation between surface tension and concentration is obtained and secondly, the surface age at which the dynamic surface tension depends most strongly on the concentration is determined.
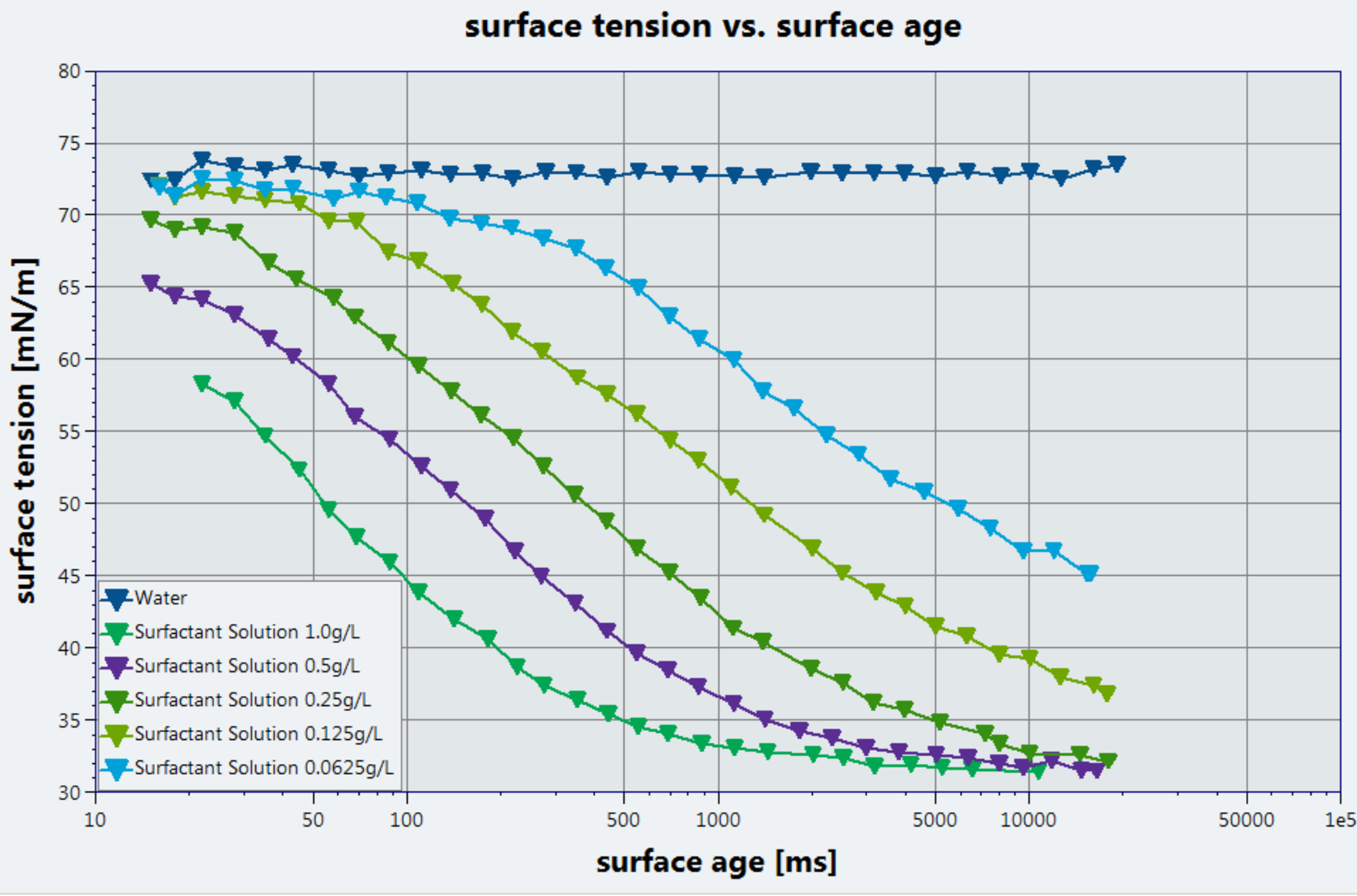
This surface age is set on the measuring instrument and used for bath control. Modern measuring instruments access stored calibration curves, display the surfactant concentration, and validate the result against previously defined limit values. In addition, they display the trend of the last measurements so that the time of a necessary subsequent dosing can be estimated. In this way, quality losses and downtimes can be prevented with little effort.