Das MSA der Firma KRÜSS ist dank verfügbarer API inlinefähig und bietet uns damit die Chance auf eine Industrie 4.0-Qualitätskontrolle.
Ringo Köpge
Wissenschaftlicher Mitarbeiter, Fraunhofer CSP
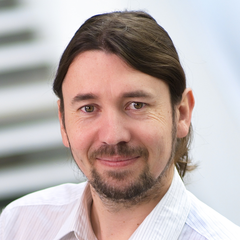
Die Solarenergie erfährt unter den erneuerbaren Energiequellen derzeit weltweit das größte Wachstum und hat bezogen auf die jährliche Gigawattleistung inzwischen die Windkraft überholt (Stand 2019, Quelle: www.bmwi.de). Einrichtungen wie das Fraunhofer-Center für Silizium-Photovoltaik CSP sorgen für eine immer effizientere und damit wirtschaftlichere Nutzung des photoelektrischen Effekts und treiben so die positive Entwicklung weiter voran. Ringo Köpge leitet als wissenschaftlicher Mitarbeiter am Fraunhofer CSP ein Forschungsprojekt zur Optimierung des Herstellungs- und Qualitätssicherungsprozesses für Wafer, welches auch die Kontaktwinkelmessung zur Reinigungskontrolle beinhaltet.
Wafer aus Silizium sind die Vorstufe gängiger Solarpanels. Sie durchlaufen nach der Herstellung des Rohwafers mehrere Ätzungsprozesse, welche durch Verunreinigungen der Oberfläche beeinträchtigt werden würden. Deshalb ist die Reinigungsendkontrolle der Wafer ein unverzichtbarer Schritt der Qualitätssicherung. Diese zu optimieren hat sich Ringo Köpge, Projektleiter am Fraunhofer CSP, zur Aufgabe gemacht. Bei der Methode für die Reinheitsprüfung entschied sich der Wissenschaftler für Benetzbarkeitsmessungen mittels der Kontaktwinkelmethode, weil die Materialprüfung berührungslos und zerstörungsfrei abläuft und bei der Verwendung reinen Wassers keine Spuren auf der sensiblen Oberfläche hinterlässt. Köpge will damit zwei wichtige Fragen beantworten: Wie kann eine erfolgreiche, möglichst viele Proben erfassende Reinigungsendkontrolle von Wafern erfolgen und wie korrelieren die dabei gesammelten Kontaktwinkeldaten mit dem Wirkungsgrad der fertigen Solarzellen?
Im Rahmen des Projektes sollte ein Modellprozess aufgesetzt werden, der nach erfolgreichem Abschluss für die industrielle Skalierung der Qualitätskontrolle des Wafering in Frage kommt. Ein inlinefähiges, schnell arbeitendes Messinstrument war dafür eine zwingende Voraussetzung, und zwar wegen des großen Probenaufkommens und damit die Messung unmittelbar nach der Reinigung erfolgen kann. Köpge entschied sich für den KRÜSS Mobile Surface Analyzer – MSA, ein von Hand bedienbares Instrument, das aber auch für den Einsatz in einem Robotersystem ausgelegt ist. Eine Schnittstelle (API) der Software des MSA ermöglicht den Remote-Start der Benetzbarkeitsmessungen und eine automatische Abfrage der Ergebnisse durch andere Software.
Die Ausstattung des Fraunhofer CSP ermöglicht es, je nach Fragestellung die gesamte Prozesskette des Wafering abzubilden. Zunächst wird ein mit Fremdatomen dotierter Silizium-Einkristall, der so genannte Ingot, gezüchtet. Dieser Siliziumblock wird mit einer Opferplatte verklebt und beides zusammen mir einer Multi-Drahtsäge in 180 bis 250 µm dicke, quadratische Scheiben zerteilt die Rohwafer. Die Optimierung all dieser Schritte, einschließlich der Entwicklung eines Klebstoffs für die Opferplatte, war bereits Teil anderer Forschungsprojekte. Je nach Fragestellung beteiligen sich auch Projektpartner an den genannten Schritten: die PVA TePla AG aus Wettenberg (Hessen) bei der Kristallisation und die Erfurter Firma PV Crystalox Solar Silicon GmbH beim Wafering.
Nach einer Vorreinigung, die den Kleber für die Opferplatte auflöst, durchlaufen die Wafer in einer automatischen Reinigungsanlage eine Reihe von Ultraschallbädern, um sie vom Siliziumstaub und organischen Kontaminationen und schließlich wieder von den Tensiden aus den Reinigungsmitteln zu befreien.
Bei der anschließenden Inline-Kontrolle und Klassifizierung in A- und B-Wafer wird u. a. die Dicke erfasst, die optische Qualität mittels einer Kamera überprüft und schließlich der Kontaktwinkel gemessen.
Die vielen Prozessschritte gehen mit einer ebenso großen Zahl an Einflussfaktoren für die Qualität des Endprodukts einher. Die maßgebliche Stromausbeute pro Fläche kann aber erst an fertigen Zellen untersucht werden, die aus den geprüften Wafern entstehen. Im Kern der Untersuchung steht die Frage, welche Prozessparameter und Qualitätsdefizite sich wie stark auswirken und was der Kontaktwinkel über die zu erwartende Leistung des fertigen Solarpanels aussagt.
Eine riesige Datenmenge ist erforderlich, um Zusammenhänge mit den vielen unabhängigen Einflussfaktoren zuverlässig zu ermitteln. Im Rahmen des Projekts bewegen sich daher tausende von unterschiedlich verarbeiteten und gereinigten Wafern durch die Stationen der Inline-Qualitätskontrolle. Für die Auswertung und Interpretation der Kontaktwinkelmessungen ziehen Köpge und seine Kollegen Methoden der Data Science heran und kooperieren dabei auch mit der Firma Kontron AIS aus Dresden. Die Ergebnisse versprechen nach einem erfolgreichen Projektabschluss wegweisend für die Optimierung und Qualitätssicherung beim Photovoltaik-Wafering zu werden.
Der Name Fraunhofer steht wie kein anderer für anwendungsnahe Forschung, welche die Entwicklung innovativer Produkte und den engen Austausch mit Unternehmen und Hochschulen in den Mittelpunkt stellt. Mit 29.000 Mitarbeiter:innen an mehr als 80 Forschungseinrichtungen und unzähligen Partnern und Auftraggebern aus der Industrie ist die Fraunhofer-Gesellschaft e. V. der größte Verband dieser Art in Europa.
Das Fraunhofer-Center für Silizium-Photovoltaik CSP in Halle wurde 2007 aus dem Institut für Mikrostruktur von Werkstoffen und System IMWS sowie dem Institut für Solare Energiesysteme ISE ausgegründet. Neben der Kristallisation und dem Wafering gehören Analysemethoden entlang der Prozesskette, das Recycling bestehender und die Entwicklung neuer Halbleitermaterialien sowie die Daten- und Prozessanalytik zu den vielfältigen Forschungsthemen am Fraunhofer CSP.