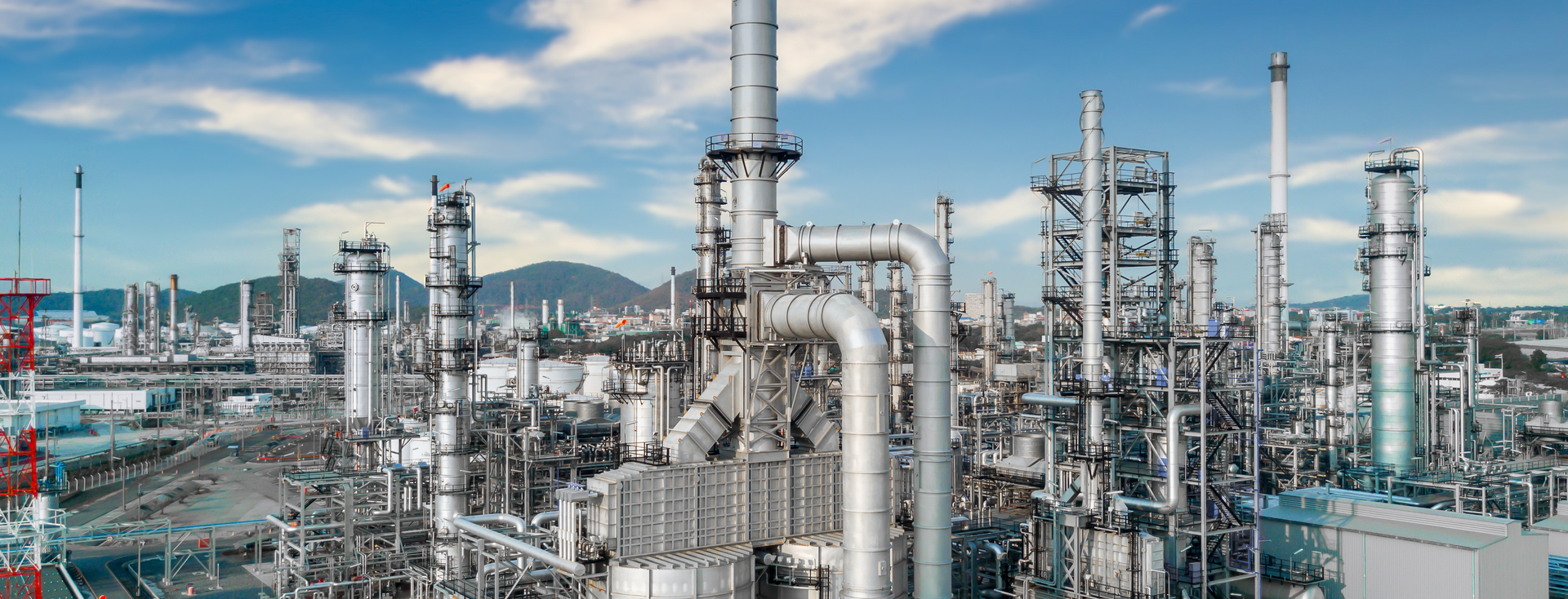
胺气处理(气体脱硫)中的消泡应用
分析发泡行为,查找原因,预防故障
未经处理的天然气和沼气在提取后不能立即使用,必须首先经过精炼过程。因为除其他物质外,这些气体还含有硫化氢(H2S)和二氧化碳(CO2)等酸性气体,这些气体在水溶液中会形成弱酸。出于以下多种原因,必须从气体混合物中去除这些物质:
- 酸性气体会加速管道和其他设备部件的腐蚀。
- 降低热能生产的效率。
- 当 H2S 燃烧时,会形成酸性更强的硫氧化物,对环境造成严重危害。这些物质也必须从化石燃料或废物焚烧(烟气脱硫)产生的烟气中去除。
为了去除 CO2 和 H2S 气体,需要在各种胺化合物的水溶液中进行胺气处理。经过这一步骤后气体不再具有化学酸性,因此该过程也被称为气胺法脱硫。这一精心设计的程序循环进行,以制备可重复使用的胺,并分离出先前结合的酸性气体。
在不久的将来,如果这种历史悠久的工艺被大规模用于捕集和封存各种工业燃烧过程中产生的二氧化碳,那么这种工艺可能会发挥更加重要的作用。
起泡--后果严重的副作用
起泡会严重影响胺处理工艺,造成严重的负面影响,轻则严重影响操作,重则导致工厂暂时完全停工。然而,纯胺溶液不会产生泡沫。只有当它们受到优质碳氢化合物及其化合物的污染时,才会形成泡沫。这些杂质会吸附在液体表面,从而降低液体的表面张力,这是产生泡沫的根本原因。
污染源不同,影响也不同
胺处理是一种逆流工艺,气体在塔内向上流动,而吸收溶液则在一系列可渗透的塔盘上向下流动。如果气体是污染源,例如由于过滤不足,泡沫最初会在塔底形成,然后从一个塔盘膨胀到另一个塔盘,在上升过程中继续污染溶液。至少在监测沿塔的压力时,这种情况是明显的,因此在泡沫到达塔顶之前仍有时间做出反应。然而,在此之前,中和气体的质量可能会受到影响,因为 H2S 尤其不易受到起泡胺溶液的约束。
向下流动的胺溶液的预污染甚至可能更严重。在这种情况下,起泡会从塔内更上层开始,很快就会导致混合物击穿(胺残留)到设备的其他部分。这不仅会严重影响生产过程,甚至会危及接触到可能泄漏的危险物质的人员。
具有讽刺意味的是,添加到胺混合物中的消泡剂往往是另外一种形式的污染源。如果添加量过大,消泡剂反而会稳定泡沫层,而不是像预期的那样破坏泡沫层。这是典型的 “解决方案反而带来了更多的问题”,因为添加更多消泡剂这种看似显而易见的措施只会使情况变得更糟。
有针对性地分析泡沫,找出原因
在实验室做预实验,有助于提前发现是否容易形成泡沫,而不仅仅是在处理过程中加以应对。在有意义的测量框架内,可以真实地模拟胺处理过程,并以可靠的数据记录泡沫形成的程度。
测量起泡性
许多工厂的操作人员已经在使用人工测量发泡性的方法进行过程监控。然而,这种测试的可重复性往往还有待提高。因为不仅仅是特定的参数(特别是气体压力)是手动调整的,泡沫高度通常也是目测的,而泡沫的衰减时间则是用秒表测量的。这种方式显然是有问题的,同时也会引入很多人为的误差,因为“好的产品”和“不好的产品”泡沫的衰减时间跨度通常在几秒钟之间。
使用动态泡沫分析仪测量仪器分析起泡性时,气体会通过具有规定孔径的过滤器底部,进入标准玻璃量筒中的液体。体积流量由电子控制,可在很大范围内精确测定。一个 LED 光柱和一排光电探测器以高分辨率测量随时间变化的泡沫高度。记录和数字存储的测量曲线具有极佳的再现性。
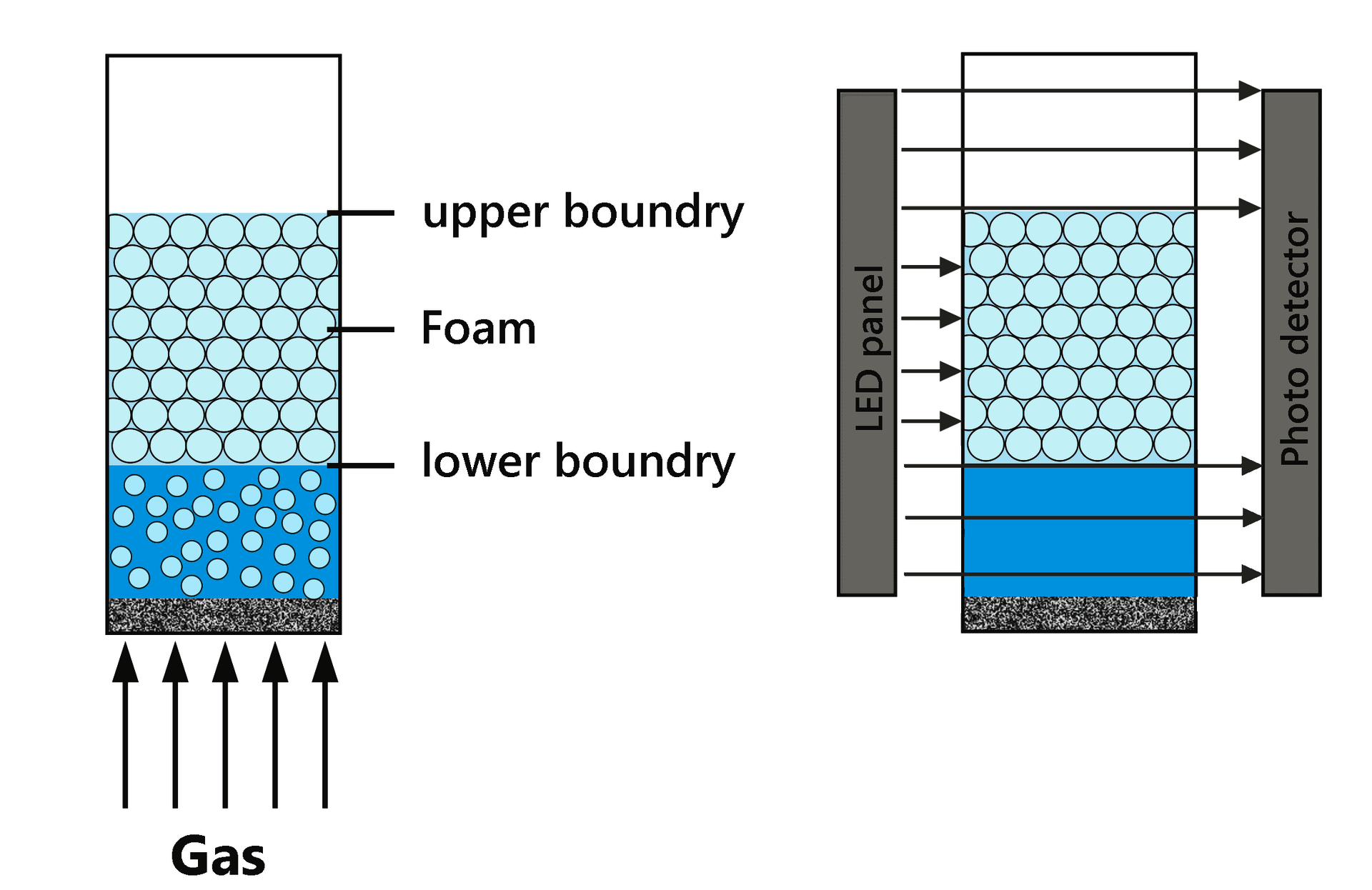
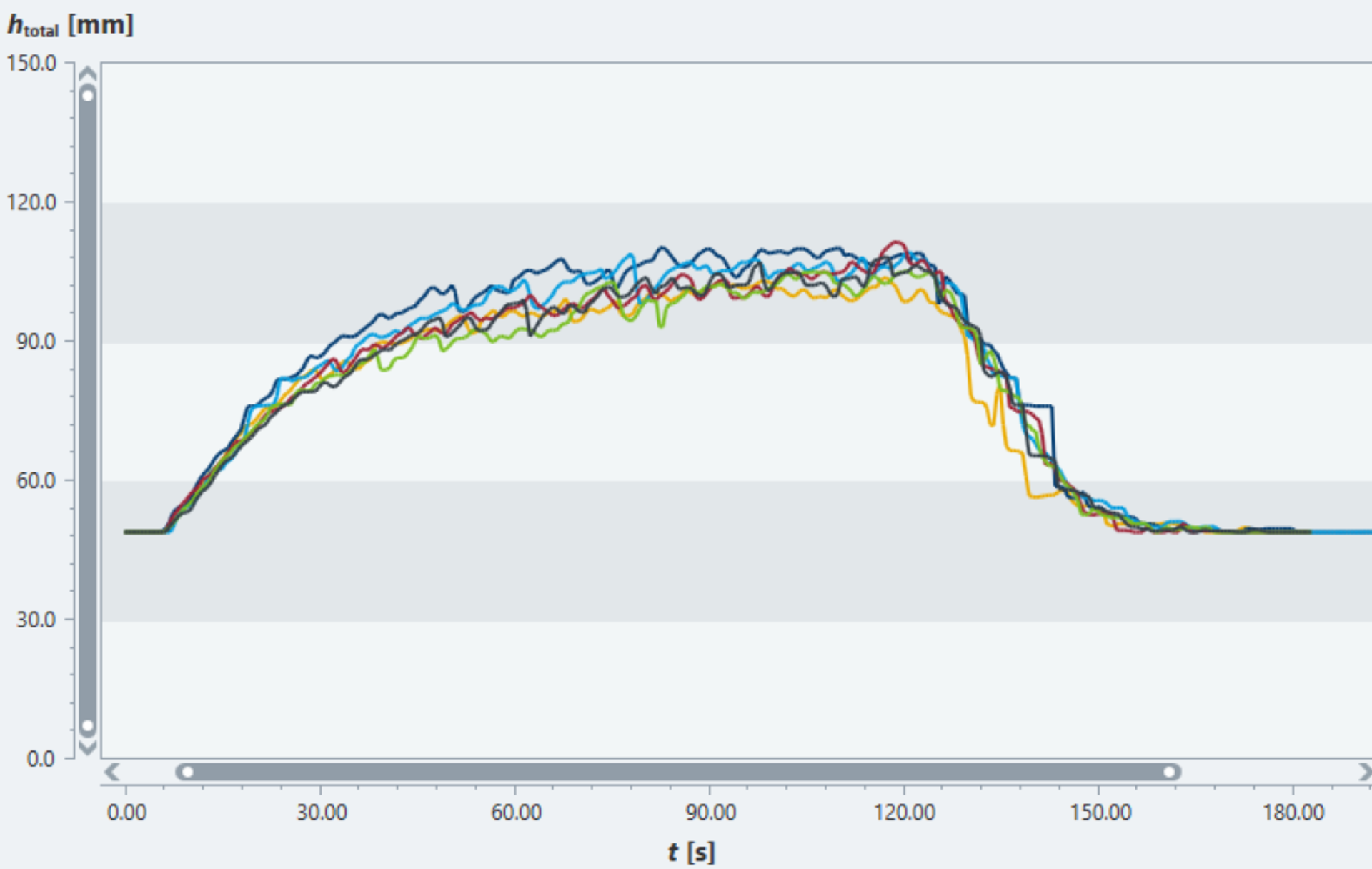
除了像标准程序那样使用空气发泡,仪器还可以使用连接外部气体发泡,也可以在实际工艺温度下进行测量,以便将结果尽可能接近胺处理过程中的条件。
据此设计的试验揭示了起泡的根源:
- 用清洁气体对用于加工的胺混合物进行发泡,以检测液体是否受到污染。在许多情况下,用空气进行测试就足以检测泡沫形成的趋势。
- 将清洁的模型混合物与实际气体混合物发泡,以检测气体中的表面活性杂质。
这样就可以确定在每种情况下,所涉及的成分(进气或吸收溶液)是否以及在多大程度上造成了起泡。
评估泡沫衰变
泡沫是否以及在多大程度上成为破坏性因素,不仅取决于起泡性,还取决于它的衰减动态。在泡沫非常不稳定的情况下,起泡和衰变之间往往会达到平衡,因此泡沫量不再增加。泡沫寿命越长,积聚的风险就越大,这种积聚会在塔内的塔盘之间扩散。这种风险会随着气体压力的上升而增加。
在所述的泡沫分析中,即使在发泡阶段结束后,也能以较高的时间分辨率记录泡沫高度,并以关键数字(如衰减半衰期)描述泡沫衰减的动态过程。泡沫量是否在增加以及增加的速度如何,也可以通过循环测量(泡沫和衰减测量的自动化程序)来分析。